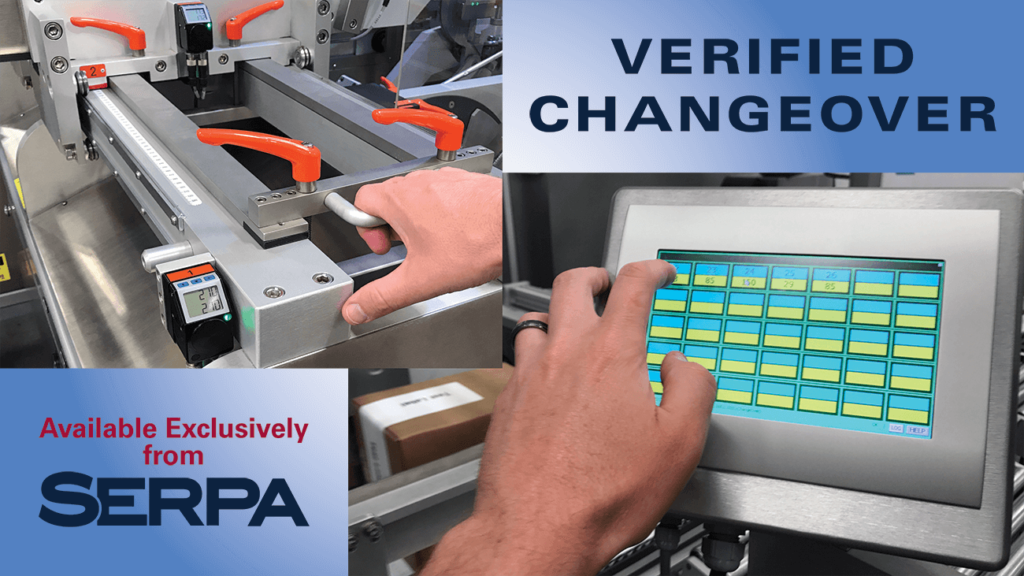
When needing to changeover lines to a new product recipe, most high-speed manufacturing and packaging machines utilize outdated changeover practices; but this method can lead to complications due to the number of required tasks and the difficulty of making the adjustments. Changeover practices are a common source of errors and low first pass yield, as steps can be overlooked and assemblies not installed correctly. When driving down the costs associated with unplanned downtime, accountability and verification play an important role in effective changeovers. Serpa has created a system to add accountability and additional verification to changeovers through user-friendly HMIs and electronic position indicators. When performing changeovers, having a PLC or software driven verification program is the only way to increase first pass yield and decrease unplanned downtime and unforeseen maintenance costs.
For assemblies requiring linear and rotary adjustments by the machine operator, Serpa has engineered a solution using a combination of electronic position indicators and touchscreen HMIs offered on each of their machines, increasing changeover reliability for all assemblies. When not correctly performed, a machine changeover causes serious problems to the product and the line.
To eliminate changeover errors, an electronic position indicator displays the current value of the changeover point, the target value, and the changeover status with an LED light. The machine program compares the values and will not allow the machine to start unless they match. That changeover point will be shown in red on the HMI and position indicator when the assembly position does not match the program position and will change to green when the assembly is moved to the correct position. Interlocking these values saves product and eliminates low first pass yield.
For assemblies where an electronic position indicator is unable to be used, an embedded scale with pointers and a digital display allows the desired adjustment to be made efficiently. The HMI display shows the target value for the changeover point and requires a button on the touchscreen to be pressed by the operator after the assembly has been moved to the target position as a means of verification. Pressing the button signals to the program that the changeover for that assembly has been completed. The operator can also press and hold their finger on the desired changeover point to view photos of the changeover location. For assemblies requiring multiple step changeovers, the operator can scroll through the photos as they perform the changeover.
Verified Changeover eliminates the need for the operator to carry paper changeover sheets, allowing them to use both hands for the tasks. This increases efficiency and reduces changeover times while eliminating errors associated with incorrect or difficult to read sheets. It is the premier solution for error free changeover by the machine operator. Not only do sites see an increase in operator efficiency, but also in equipment availability, flexibility and changeover reliability. And as an added benefit, it allows maintenance and engineering to skip reviewing all of the changeover points before beginning to troubleshoot any issues the machine may be experiencing.